Key Advantages and Considerations of Executing Plastic Extrusion in Your Projects
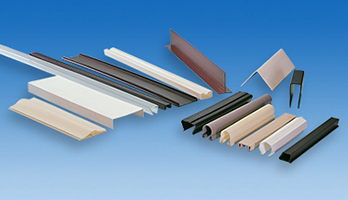
Recognizing the Basics of Plastic Extrusion
Plastic extrusion, a staple in the production industry, is a process that includes melting raw plastic material and improving it right into a constant profile. This profile, once cooled, can be reduced right into wanted lengths or curled for later usage. The beauty of plastic extrusion hinges on its convenience. A vast array of products, from piping to window frameworks, can be generated. The process requires an extruder, an elaborate device with a warmed barrel, a rotating screw, and a die at the end. The plastic product, in the kind of pellets, is fed right into the extruder, where it's thawed and forced with the die, taking its shape. The selection of plastic and the layout of the die figure out the product's characteristics.
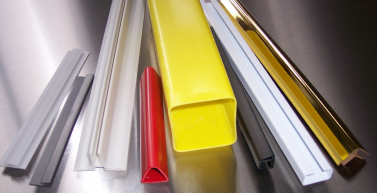
The Economic Benefit of Plastic Extrusion
The economic benefit of plastic extrusion exists mostly in 2 areas: economical material production and valuable production speeds. With plastic extrusion, companies can generate high quantities of material at a lower price compared to various other methods. The procedure boasts an outstanding manufacturing speed, substantially minimizing time and further enhancing its economic feasibility.
Cost-efficient Material Production
A considerable benefit of plastic extrusion is its remarkable cost-effectiveness. Furthermore, the extrusion procedure permits for a high level of precision in forming the plastic, decreasing the demand for pricey post-production modifications or adjustments. All these factors make plastic extrusion a highly affordable option for many projects, using an appealing equilibrium in between cost and performance.
Beneficial Manufacturing Speeds
While preserving the cost-effectiveness of the products, another significant advantage of plastic extrusion exists in its rapid manufacturing rates. This combination of cost-effectiveness, speed, and high quality highlights the substantial financial benefit of implementing plastic extrusion in numerous projects.
Convenience and Personalization: The Toughness of Plastic Extrusion
One of the noticeable staminas of plastic extrusion depends on its flexibility and personalization potential. These high qualities unlock to endless style possibilities, giving manufacturers the capacity to customize items to details needs. This heightened level of personalization not only boosts product performance but also significantly boosts product originality.
Unrestricted Layout Opportunities
Plastic extrusion shines in its capability to provide virtually infinite design opportunities. This technique supplies flexibility to develop detailed accounts and complex forms, a feat difficult to accomplish with various other fabrication techniques. Owing to the liquid nature of liquified plastic, the process is versatile enough to produce a varied variety of dimensions, measurements, and types. The plastic can be manipulated to match one-of-a-kind specs, enabling the production of personalized geometries and conference details customer needs. Plastic extrusion can manage a selection of plastic types, expanding its application extent. This versatile technique, for that reason, offers a vast array of markets from construction to auto, packaging to electronic devices, and beyond. With plastic extrusion, the design opportunities are basically unlimited.
Increasing Item Uniqueness
The convenience of plastic extrusion can greatly improve item uniqueness. This process allows developers to try out various shapes, dimensions, and shades, providing the freedom to produce special products that stick out out there. It is this customization that offers an unique identity per product, differentiating it from its rivals.
Along with its aesthetic benefits, the customizability of plastic extrusion additionally provides practical advantages. Developers can change the buildings of the plastic according to the certain demands of the application, improving the item's functionality. They can make the plastic much more flexible, much more resilient, or extra immune to warmth, depending on what the check over here product calls for. Thus, plastic find here extrusion not just improves product individuality yet additionally its energy and marketability.
Layout Limitations in Plastic Extrusion: What You Required to Know
Exactly how can design restrictions possibly affect the process of plastic extrusion? While plastic extrusion is functional, design limitations can stop its advantages. Certain facility designs might not be feasible because of the limitations of the extrusion procedure, possibly limiting the creation of elaborate profiles. The process is less ideal for multi-chambered or hollow frameworks. Additionally, the extrusion process may not always provide the preferred surface area coating, specifically for those calling for high gloss or optical clarity. Material choice can additionally pose challenges, as not all polymers appropriate for extrusion. High-temperature immune plastics, as an example, may present difficulties. Understanding these restrictions is crucial for effective application of plastic extrusion in your jobs. plastic extrusion.
Assessing the Ecological Impact of Plastic Extrusion
While understanding layout this constraints is a significant element of plastic extrusion, it is similarly crucial to consider its environmental implications. The process of plastic extrusion includes melting plastic products, potentially releasing hazardous gases into the setting. Better, the resulting items are typically non-biodegradable, contributing to landfill waste. Nonetheless, improvements in modern technology have actually enabled for more environmentally-friendly techniques. Utilizing recycled plastic products in the extrusion process can reduce ecological effect. Furthermore, creating biodegradable plastic options can help alleviate waste problems. Assessing these ecological elements is essential when carrying out plastic extrusion tasks, guaranteeing an equilibrium between performance, cost-effectiveness, and environmental responsibility.
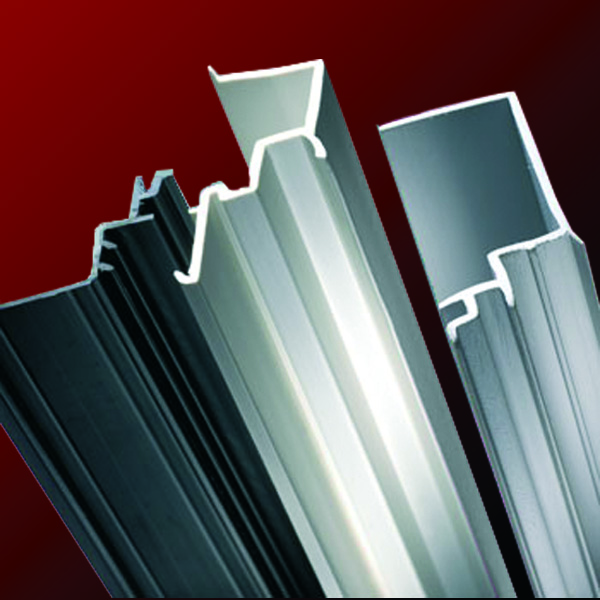
Case Research Study: Effective Projects Making Use Of Plastic Extrusion
Success tales in the area of plastic extrusion abound, showing both the convenience and performance of this production process. plastic extrusion. An additional successful case is the manufacturing of plastic movie for packaging and farming. These instances illustrate plastic extrusion's critical function in numerous industries, proving to its versatility, cost-effectiveness, and dependable output.
Verdict
Finally, plastic extrusion provides a efficient and affordable technique for generating complicated forms with minimal waste. While it gives various advantages such as cost-effectiveness and adaptability, it's important to take into consideration prospective layout restrictions and ecological effects. Applying recycled or naturally degradable materials can mitigate these problems, boosting sustainability. Incorporating plastic extrusion into tasks can result in effective outcomes, as evidenced by various study.
Plastic extrusion, a staple in the manufacturing sector, is a process that involves melting raw plastic product and reshaping it into a constant account. Plastic extrusion can take care of a variety of plastic types, broadening its application extent.Just how can design limitations potentially impact the procedure of plastic extrusion? The procedure of plastic extrusion entails melting plastic products, possibly launching damaging gases right into the atmosphere. Utilizing recycled plastic materials in the extrusion process can minimize ecological influence.